

As a result, it has been found during research on such connections (Willibald et al., 2003a, 2003b) that the maximum weld length possible, inside a square hollow section, is roughly 1.2 times the height of the section (or the arm length of the welder) to avoid a severe loss in welding quality. All welding has to be done from the open end of the HSS and the operating room for the welder is restricted to just half of the HSS void. Welding of the inserted plate to the inside of the HSS is achieved by four fillet welds (Figure 3), which will be loaded in shear parallel to the axis of the weld. This hidden connection concept can be applied to round, square and rectangular HSS members, but there are member size limitations.įigure 3: Fillet weld to the inserted plate
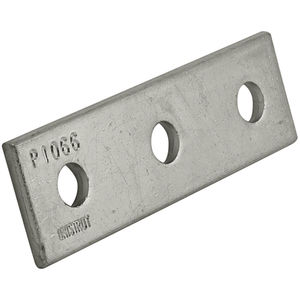
The joint between the cover and the HSS can even be sealed by caulking, giving the appearance of a welded joint. One method for holding the thin cover pieces in place is to use small fasteners through the metal that screw into threaded bars extending from the splice plates. With the plate welded to the inside of the un-slotted HSS, rather than protruding beyond the HSS width, the bolted lap splice can be completely hidden, after bolting up, by a (non-structural) cover in the shape of two half-HSS pieces, as shown in Figure 2. The hidden splice plate connection is also described in STI (2017), as an “interior splice plate” connection. These two alternates are illustrated in Figure 1. If the need for an invisible bolted splice connection arises, a hidden splice connection may be possible (since there are fabrication and strength limitations) in lieu of the similar slotted HSS lap splice connection (case (ii) above).
#CONCEALED SPLICE PLATE CODE#
AESS is covered in Section 10 of AISC 303-16, the Code of Standard Practice (AISC, 2016a).įigure 2: Hidden lap splice connection, with cover Both, however, may be considered unacceptable if aesthetics are important and an architecturally exposed structural steel (AESS) category is sought. Case (ii) is particularly suited to axial loading, places the bolts in shear, but produces shear lag in the HSS as only two walls of the HSS are connected to the inserted plate. Case (i) is popular for combined axial force and moment loading combinations, but places the bolts in tension – with the bolt force amplified due to prying action – under axial tension loading in the HSS. Standard, bolted, splice connections between HSS members are commonly achieved using: (i) a flange plate welded to the end of the member, with the bolts located beyond and around the perimeter of the HSS or (ii) a plate welded into a slotted HSS, with the bolts located beyond the end of the HSS in a lap splice connection. Figure 1: Alternate bolted lap splice connections: with the plate welded into a slot in the HSS (left), and with the plate welded inside the HSS (right)
